Food and beverage manufacturers operate in a world where every hour counts. When your facility is undergoing renovations, expansions, or infrastructure upgrades, production can’t stop, and delays aren’t just costly, they’re unacceptable. The challenge? Executing construction in a live, sanitary, tightly regulated environment without disrupting the flow of operations.
At CSM Group, we understand this challenge better than anyone.
Why Downtime Is the Real Cost Driver
In our experience managing hundreds of capital projects in food and beverage facilities, the biggest risk isn’t necessarily construction cost—it’s unplanned operational downtime. Shutting down a packaging line or disrupting sanitation schedules can cost tens of thousands of dollars an hour, delay shipments, and damage customer relationships. For that reason, our construction strategy prioritizes continuity of operations above all else.
Construction Without Disruption: Our Proven Approach
CSM Group has developed a playbook for executing construction projects in operational food facilities with zero unplanned interruptions. Here’s how we do it:
Preconstruction Planning with Production at the Core
We don’t start with blueprints—we start with your production schedule. Our teams work together with plant managers, sanitation supervisors, and operations teams to map out construction phasing that aligns with your throughput, changeovers, and clean-in-place (CIP) cycles. We develop multi-shift strategies to minimize overlap and avoid peak production hours.
Rigorous Safety and Sanitation Controls
Construction activity introduces risk, especially in facilities governed by FSMA, USDA, or SQF standards. Our team implements containment protocols, including hard wall separations, negative air pressure, debris management, and daily clean-downs—often exceeding regulatory bodies' baseline expectations. We also train every subcontractor to understand and adhere to food safety practices because compliance doesn’t stop at the production floor.
Collaborative Scheduling with Live Data
Our construction managers use digital tools and real-time dashboards to maintain constant visibility into project progress. We track every milestone, coordinate utility shutdowns in collaboration with facility maintenance teams, and make sure schedule updates are communicated across departments daily. The result? Predictable timelines and zero surprises.
Agile Response to the Unexpected
Food facilities don’t shut down for construction, and we don’t expect them to. When changes happen (and they do), we respond immediately. Whether it's a shift in sanitation timing or a mechanical failure, our teams are on-site, in sync, and empowered to adjust course while maintaining forward momentum.
Built on Trust—and Results
Our clients in the food and beverage industry, from global consumer brands to regional processors, count on CSM Group to execute complex construction projects without disrupting their business. We’re proud of our reputation for delivering:
- Seamless plant expansions
- Critical equipment installations
- Infrastructure and utility upgrades
- Production line relocations
—all while operations continue safely and efficiently.
Let’s Build Without the Shutdown
Construction in food manufacturing is never just about steel and concrete. It’s about protecting your brand, product, and production goals. At CSM Group, we deliver construction management solutions that work with your operations, not against them.
Let’s discuss your next project—and how we can keep your production line moving forward.
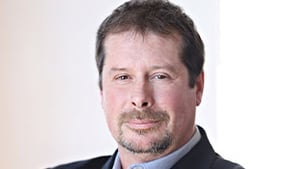